Technics
Representing technical interests
CETOP is also active in the field of the representation of technical interests, for example in the area of European Directives and the effect of these on the fluid power industry. With its Technical Commission, CETOP can draw on an excellent network of technical experts who discuss these subjects whenever necessary from the point of view of the fluid power industry. They produce statements or “Position Papers“.
What is Fluid Power and what does it do?
Fluid power – hydraulics and pneumatics – transmits force and power for drive, control and motion functions. Unlike electrical power transmission engineering, it uses the physical characteristics of a fluid such as oil, synthetic fluids, water, and air, to transmit force and power. We come across it in all aspects of our daily lives. Hardly any product is developed without the use of fluid power, and barely a machine or aircraft moves without it; we are just not aware of it most of the time.
Hydraulics and pneumatics manufacturers are suppliers for the entire manufacturing industry. Customer sectors include, for example, the automotive industry, the construction and agricultural machinery industry, conveying technology, manufacturers of food and packaging machines, woodworking and mobile machines, machine tools and printing machines, as well as electrical engineering, ship building, smelting plants and rolling mills, through to aviation and space travel, medical technology, environmental technology, the rubber and plastics industry, chemicals, electronics and semiconductor industry. Innovative developments of fluid power components and systems involving the latest materials and state-of-the-art electronics as well as motion and control systems are giving added impetus to technological progress.
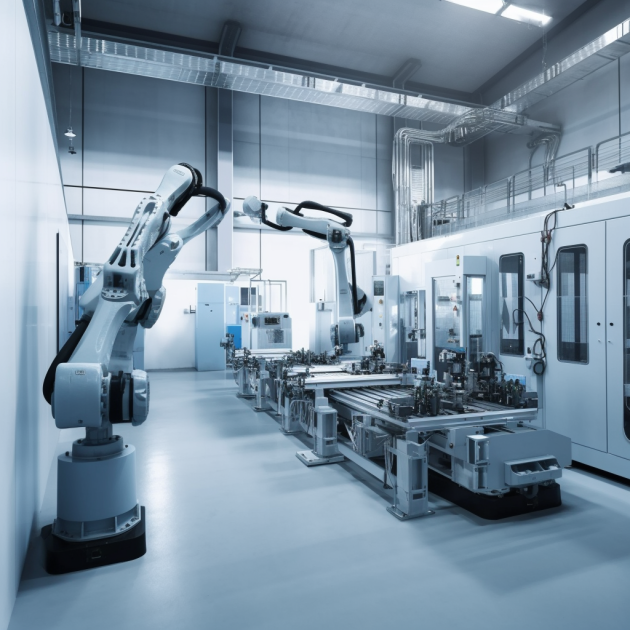
Pro Hydraulics
- High power density
- Robustness and overload protection with simple load limitation
- Good time response due to low inertia
- Small installation space and flexible assembly
- Long life-time
- Low life-cycle-costs (cost advantage with many axes due to shared hydraulic power supply unit, very cost-effective in load holding operation)
- Peak load coverage via storage technology
- Good lubrication and corrosion protection by means of an operating medium (integrated cooling)
- High starting torques with hydrostatic transmissions
Pro Pneumatics
- Robustness and overload capacity
- Simple design and lightweight construction by use of aluminum and plastics
- Low investment costs
- High specific power density
- Constant peak load
- Resilience in case where maximum power rating is exceeded (service robots)
- Low energy consumption in long cycles
- Small installation space
- Application in hazardous areas
Fluid power – powerful and precise
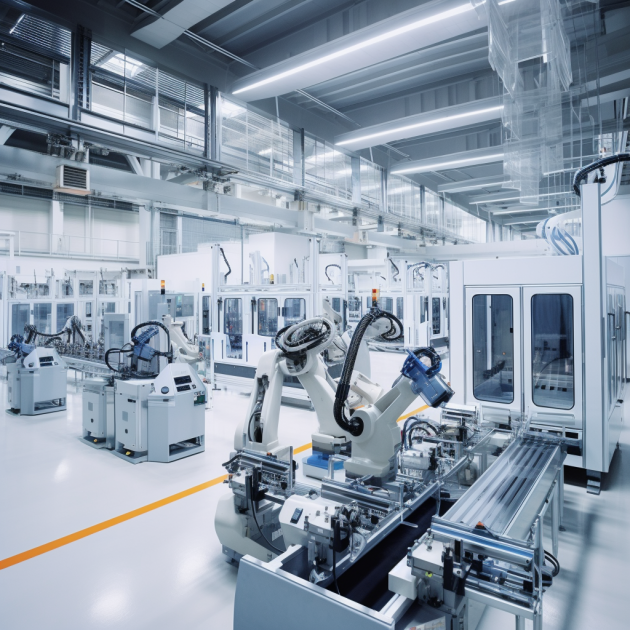
The dynamics of machines and plants is often the result of hydraulic and pneumatic power transmission and control technology. For linear and rotary movements, even lifting or lowering movements, acceleration requirements, transferring power or positioning and holding in position, hydraulic and pneumatic components are used in almost all areas of industry.
In competition with other forms of power transmission engineering, the outstanding feature of hydraulics is their particularly high power to size ratio, while pneumatics epitomise speed and compactness. Due to their cost efficiency and easy handling and assembly, they are unbeaten in a large number of applications.
The low power-weight ratio and the high power-to-size ratio mean that hydraulics are predestined for mobile applications, such as in construction machinery, agricultural machinery and communal machines. They also allow the generation of high forces and torques at low speeds and rotational speeds in stationary applications, such as machine tools and plastics machinery. Braking procedures are easy to perform without causing wear and tear. The braking energy can easily be stored and fed back to the system as and when required. In combination with electronic regulation systems, positioning accuracy can be achieved that are the equal of any electrical drive. This enhances the performance of machines, increases customer benefits and allows the constant development of new applications.
What about pneumatics with air as a working agent? It is now an inseparable part of automation. It is synonymous with dynamics, speed and
productivity in the smallest area, and therefore an integral element of all renowned sectors of the manufacturing industry.
However, even in the clean room, where top quality and cleanliness in production are crucial, pneumatics contributes to economic efficiency, be it in medical technology, in the production of chips and printed circuit boards, in the dispensary or in food processing. The range of uses is multifarious, ranging from assembly and handling tasks through feeding and positioning tasks to joining, sorting and test processes. Thanks to electronic control systems, pneumatics have long been able to travel not only to final stops but also to intermediate positions, be it in linear or rotary movements.
Fluid power – controls production processes
Intelligent control and motion today always involves integration into existing or new networks, be it on the field bus level in mechanical engineering or in all-encompassing networks.
The decentralised intelligence of actuators and sensors is increasing. Data required by quality assurance, for example, can be called up online. The operating hours counter of the compressed air system or hydraulic assembly can be read on a PC. All such tasks that in themselves are small but taken together have a significant impact on the productivity of a system can be performed cost-effectively by means of networking.
However, intelligent control and motion begins in the planning and design stage. Numerous software programmes support users in designing hydraulic
and pneumatic systems, dimensioning cylinders, grabs, vacuum suction equipment, valve terminals. Even complete assembly and handling
systems can be dimensioned, and simulated in the planning stage to assess functionality. The “Plug & Play” concept of the PC world is thus being adapted to “Plug & Work” in automation technology.
Fluid power – serving our environment
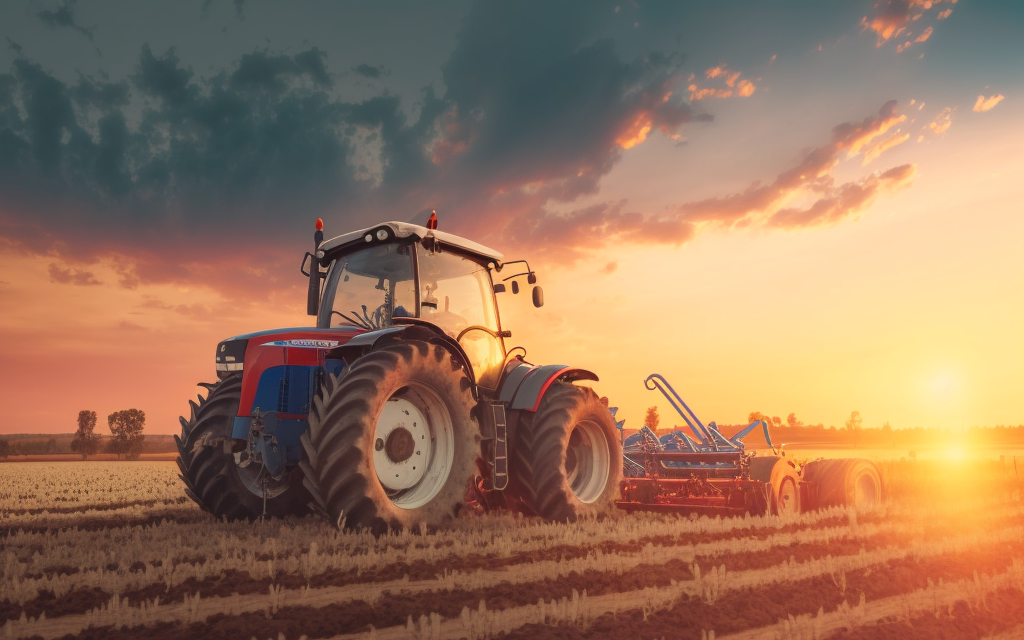
Technology, people and the environment are not mutually exclusive. On the contrary, innovative technologies, investment and the creativity of people are today shaping our future. A rapidly growing world population and scant resources are the challenges we must face.
The challenges placed on us increase not only due to the increased pressure of competition, but increasingly due to the environmental impact and our objective of offering as many people as possible a decent world to live in.
Fluid power is used in a number of applications with a view to preserving the environment: in wind power stations to move the rotor blades into the optimum wind position, in conventional power stations for flue gas desulphuration, in waste disposal and in recycling, in water treatment, in sewage treatment and in agriculture and forestry. Fluid power reliably controls procedures and processes that will safeguard the future of our environment.
Future-proof automation and drive systems
Future-proof automation and drive systems Fluid power is excellently equipped for the future. Thanks to the ease with which it is possible to link its components with electronic control mechanisms, the high power-to-size ratio and the optimisation of component sizes made possible by technical progress, it will always be a driving force. Increasingly efficient sensors, modern bus systems, ergonomic operating and diagnostic systems combine fluid power with electronics to form futureproof automation and drive systems for the requirements of tomorrow.
The boundaries between motion, drive and automation are becoming increasingly blurred and the integration of communicative components is
increasing productivity. Fluid power is taking account of this and producing new technologies such as the microsystems technology and mechatronics.
Fluid power focuses on the integration of functions and the reduction of external interfaces and contributes to energy efficiency. Customers are concentrating more and more on their core competence and therefore require ready-made and tested subsystems instead of individual components. This
saves time and costs in their process chain, but also increases the requirement for high-quality customer relations
management – a challenge fluid power is happy to take on board.
Energy and Resource Efficiency – Efficient Fluid Power
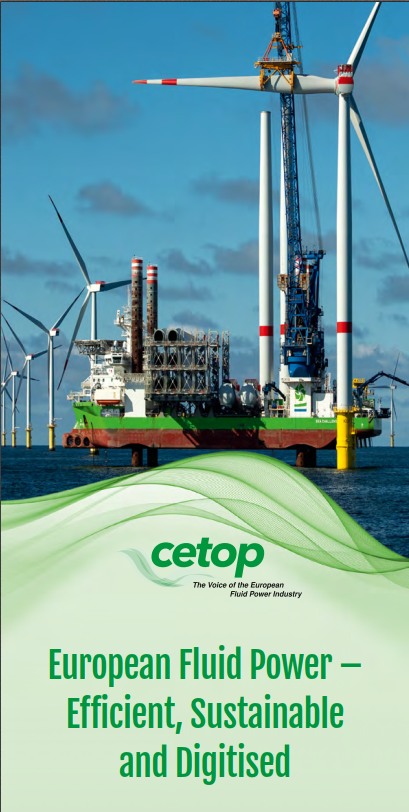
Against a background of a world shortage of energy and raw materials and the resulting sharp price increases, the energy and resource efficiency of
machines and installations is becoming ever more important. Fluid power as a high-performance technology for the creation of drive solutions is playing a very active role in this process of continuous improvement. It has been clear for some time that we need to be economical in our use of energy and material resources. The reasons, too, are long since familiar and are indivisibly linked to the way in which our energy needs are met today and have been met in the past.
There is also a move towards a new approach to the problem from the financial point of view: In considerations of the total cost of ownership over the entire life of a product, energy costs are increasingly at centre stage.
The only currently viable alternative way of reducing energy costs is energy saving, or in other words higher energy efficiency.
How can this be achieved most effectively?
It is important to achieve further increases in degrees of efficiency, for example by minimising frictional and throttling losses, etc. Flexible
application drives and dynamically optimised systems offer considerable potential for savings. With regard to all the various types of machine drives, there is, in addition to energy recovery, a second alternative way of, for example, reducing reactive power losses.
The relationship between the power consumed in pursuit of the actual purpose of a machine (for example, workpiece handling) and the power consumed by the machine it-self (e.g. overcoming motor inertia, moving gripper tools, etc.) can be optimised. One welcome side-effect
of this optimisation process is that the resulting “slimmed-down” system becomes considerably more dynamic – many drive-technology applications
could not be realised without optimised drives of this kind.
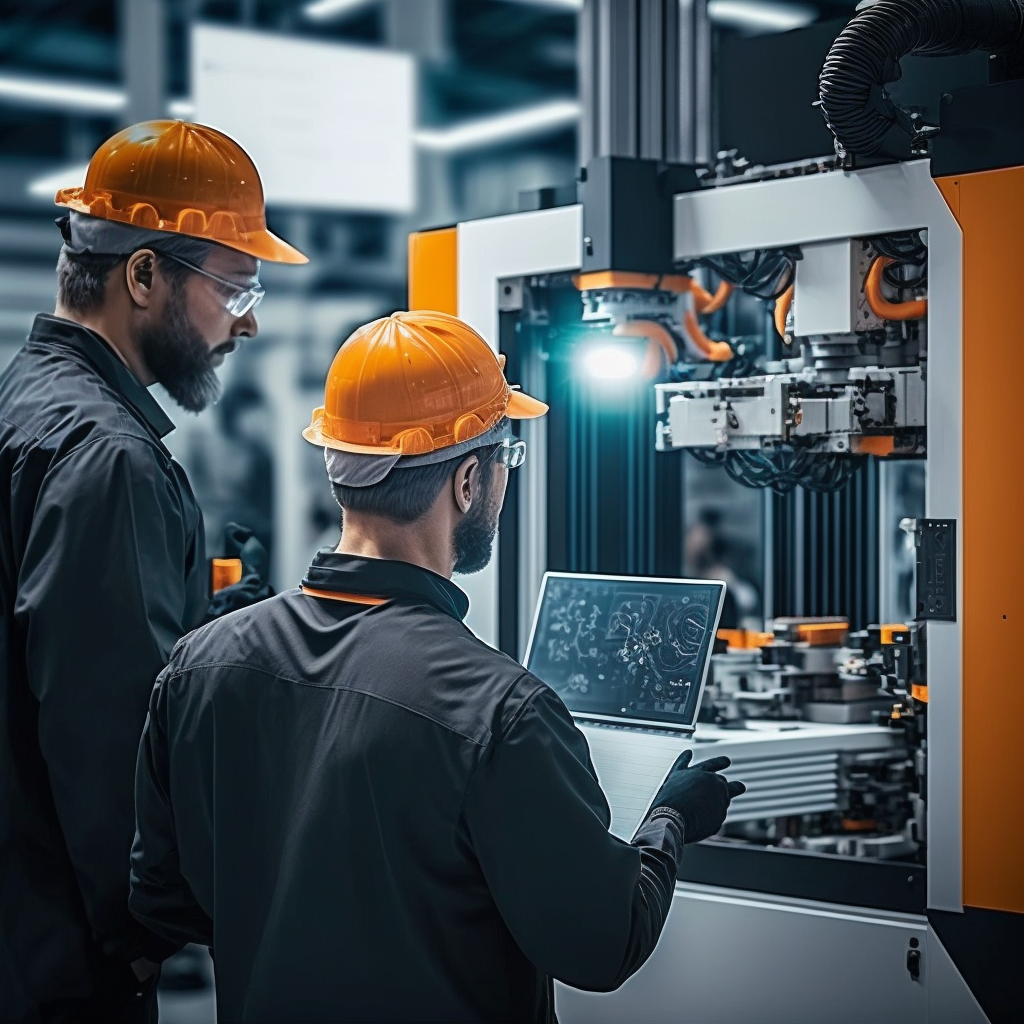
CETOP Position Papers
The Single European Market makes it necessary, among other things, to harmonise national regulations, directives and standards, with the aim of eliminating restrictions or barriers to trade.
This is achieved through European Directives, which are then enacted as national legislation by each EU member state.
Fluid power components and systems may fall within the scope of a number of European Directives, such as the Machinery Directive, the Directive on
Electromagnetic Compatibility, the Pressure Equipment Directive, the ATEX Directive, the WEEE and ROHS Directives, the Eco-design Directive and REACH regulation. CETOP interprets the Directives and their requirements with regard to their consequences for fluid power components and systems. CETOP Position Papers are published for some of the Directives which affect the fluid power industry.
CETOP Technical Commission
Excellent network of technical experts Survey of the European regulation and its impact on the Fluid Power industry Lobby at the European Commission – harmonized pan European proposals are a vital requirement for success. CETOP is the voice of the Eurpean Fluid Power industry.
Position Papers – industry’s response to EU Directives and their impact upon the Fluid Power sector.
The Technical Commission is responsible via the Vice President for Technics to the PRESIDENT’S COUNCIL, in turn the Presindent’s Council reports and consults with the CETOP Association members who form the GENERAL ASSEMBLY.